LQATS Distribution Center DC Outbound Quality Audit
Distribution Center DC Outbound Quality Audit is a process that verifies the quality of goods leaving a distribution center (DC) to ensure they meet specific standards before reaching customers or retail locations. DC Outbound Quality Audit helps reduce errors, prevent product damage, and maintain customer satisfaction. Here’s a general outline of an DC outbound quality audit process:
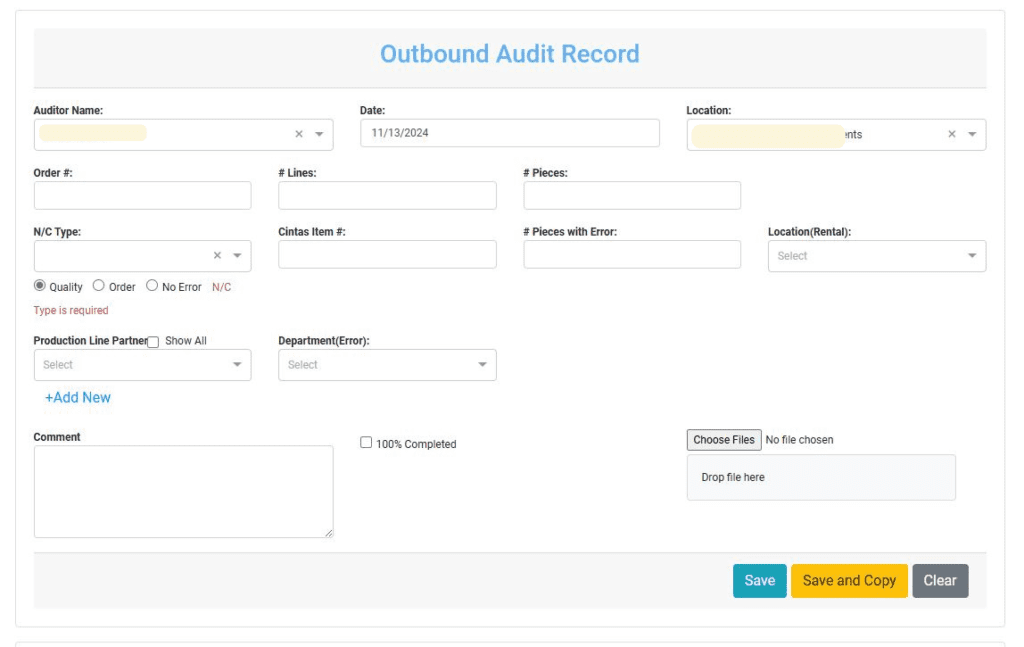
1. Distribution Center DC Outbound Quality Audit Sample Selection
Select samples from outbound shipments based on factors like order size, product type, or destination. Samples are often chosen at random but can be targeted based on known issues or risk factors.
2. Inspection Criteria
Establish clear standards for quality. Common criteria include:
- Packaging Integrity: Check for any damage or improper packaging.
- Label Accuracy: Verify product labels, addresses, and barcodes for accuracy.
- Product Condition: Inspect items for damage, cleanliness, and shelf life (for perishable goods).
- Quantity Accuracy: Confirm the correct number of items are packed.
3. Audit Procedures
- Conduct thorough checks against the criteria, noting any defects, discrepancies, or damages.
- Track metrics like defect rates, accuracy rates, and frequency of issues to identify trends.
4. Documentation
- Record all findings in a report for transparency and follow-up.
- Include details such as item SKU, quantity, type of defect, and corrective action taken (if any).
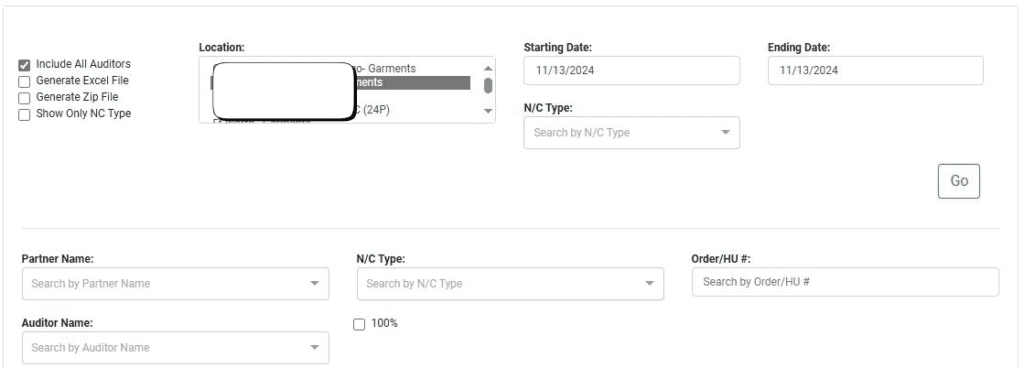
5. Feedback and Corrective Action
- Share audit findings with relevant teams for immediate corrective action.
- Implement feedback mechanisms to help reduce recurring issues, such as additional training, process adjustments, or vendor reviews.
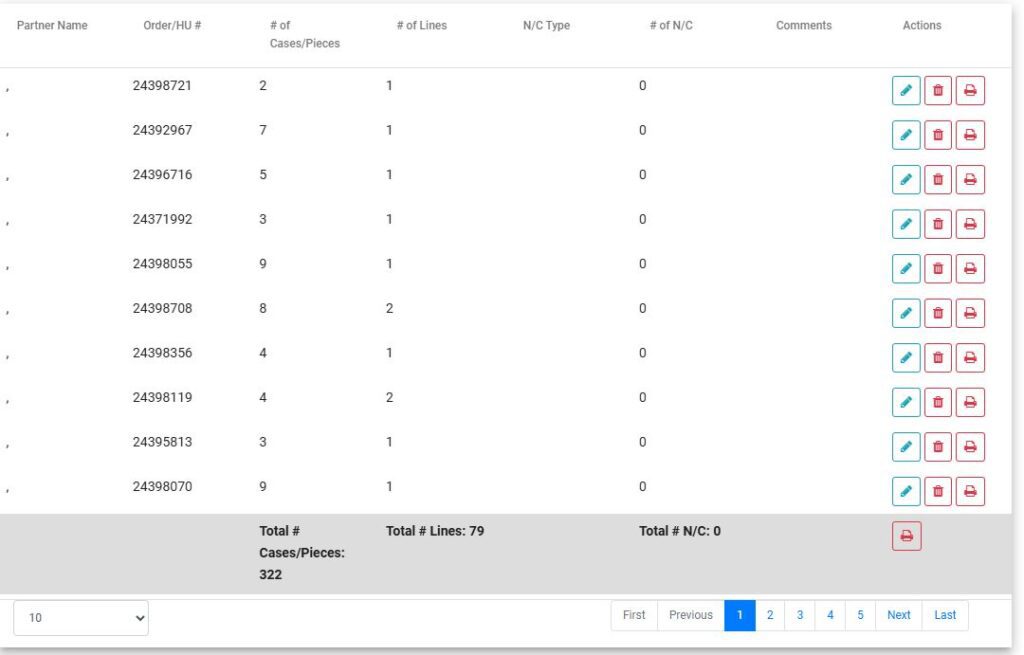
6. Distribution Center DC Outbound Quality Audit Review and Continuous Improvement
- Regularly review audit data to identify systemic problems or trends.
- Use these insights to improve outbound processes, such as updating packaging guidelines, refining picking processes, or improving training for staff.
By implementing an outbound quality audit, a distribution center can significantly improve the accuracy and condition of its outgoing shipments, enhancing overall customer satisfaction and operational efficiency.