Cleanroom Audit with Lyons Quality Audit Tracking System (LQATS)
Cleanroom Audit with Lyons Quality Audit Tracking System
Manufacturing cleanroom audit with Lyons Quality Audit Tracking System (LQATS) are essential processes to ensure that the products being produced meet required quality standards and are free from contamination. These audits are particularly critical in industries where cleanliness and product integrity are paramount, such as pharmaceuticals, biotechnology, microelectronics, and aerospace.
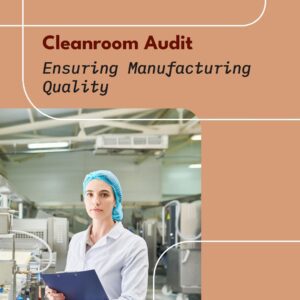
A cleanroom is a controlled environment that is designed to minimize contamination from particles, dust, microbes, and other airborne pollutants. These environments are used in various industries where even small levels of contamination can have significant consequences, such as pharmaceuticals, biotechnology, electronics manufacturing, aerospace, and healthcare.
Cleanrooms impose stringent requirements for air quality, temperature, humidity, and pressure control to maintain cleanliness levels within specified limits. Standards such as ISO (International Organization for Standardization) and Federal Standard 209E classify the level of cleanliness by specifying the maximum allowable concentrations of particles per cubic meter of air at designated particle sizes.
Key features of a cleanroom include:
Controlled Airflow:
Specialized HVAC (Heating, Ventilation, and Air Conditioning) systems provide filtered air to maintain a clean environment in cleanrooms. Engineers carefully design airflow patterns to minimize the spread of contaminants.
High-Efficiency Particulate Air (HEPA) Filters:
Cleanrooms utilize HEPA filters to remove airborne particles and microorganisms from the air. These filters efficiently capture particles as small as 0.3 micrometers.
Sealed Construction:
Construction teams build cleanroom facilities with materials and finishes that are easy to clean and maintain. They use sealed joints and smooth surfaces to minimize particle accumulation.
Gowning Procedures:
Personnel entering cleanrooms must follow specific gowning procedures. They wear cleanroom garments, including coveralls, gloves, masks, and hairnets, to prevent contamination from human skin and clothing.
Environmental Monitoring:
Cleanroom operators continuously monitor air quality, temperature, humidity, and pressure using sensors and monitoring systems to ensure that conditions remain within specified limits.
Cleanrooms are classified into different classes or grades based on the level of cleanliness required for the specific application. The classification system defines the maximum allowable concentration of particles per cubic meter of air at specified particle sizes. Cleanroom classifications range from ISO Class 1 (the strictest) to ISO Class 9 (the least strict).
Overall, cleanrooms play a critical role in industries where maintaining a controlled environment is essential for product quality, safety, and compliance with regulatory requirements.
Here’s an overview of how manufacturing product cleanroom audit is typically conducted in cleanroom environments
Preparation and Planning:
Before conducting the cleanroom audit, the audit team first develops a detailed plan that outlines the objectives, scope, and criteria for the audit. In this plan, they include identifying key areas for assessment, such as production processes, equipment, personnel practices, and environmental controls. By doing so, they ensure a comprehensive approach to the cleanroom audit.
Gowning and Access Control:
Moreover, personnel participating in the cleanroom audit must adhere to strict gowning procedures and access controls to minimize the risk of introducing contaminants into the cleanroom environment. Specifically, this may involve wearing specialized cleanroom garments, undergoing gowning training, and passing through air showers or airlocks before entering the cleanroom.
Inspection of Production Processes:
Subsequently, the cleanroom audit team observes and evaluates various stages of the manufacturing process to ensure compliance with standard operating procedures (SOPs), quality control measures, and regulatory requirements. In particular, they examine equipment cleanliness, material handling practices, product assembly procedures, and environmental monitoring data to confirm adherence to standards.
Sampling and Testing:
During the cleanroom audit, team members collect samples of in-process and finished products for laboratory testing and analysis. This process helps them verify product quality, purity, and performance according to specified criteria. Furthermore, testing methods may include particle counting, microbial analysis, chemical assays, and product functionality tests to ensure thorough evaluation.
Documentation Review:
In addition, the cleanroom audit team reviews documentation related to manufacturing processes, quality records, batch records, calibration certificates, and validation reports. This review aims to ensure completeness, accuracy, and compliance with regulatory standards. Consequently, they note any discrepancies or deviations from established procedures for further investigation.
Personnel Training and Competency:
Next, the cleanroom audit team assesses the competency of personnel involved in manufacturing operations to ensure they are adequately trained in cleanroom protocols, procedures, and safety practices. To achieve this, the assessment may include reviewing training records, conducting interviews, and observing employee behavior in the cleanroom environment.
Environmental Monitoring:
Furthermore, the cleanroom audit team monitors the cleanliness of the cleanroom environment in real time using particle counters, microbial samplers, and other monitoring equipment. If they identify any deviations from acceptable cleanliness levels, they investigate these issues and take corrective actions as necessary.
Closure and Reporting:
Finally, once the cleanroom audit is complete, the audit team documents the findings in the Lyons Quality Audit Tracking System. This documentation details observations, findings, non-conformities, corrective actions, and recommendations for improvement. Typically, management and relevant stakeholders review this report to address any identified issues and prevent recurrence in future manufacturing operations.
Overall, manufacturing product audits in cleanrooms play a crucial role in ensuring product quality, compliance with regulatory requirements, and maintaining the integrity of cleanroom environments. By identifying and addressing potential sources of contamination and process deviations, these audits help mitigate risks and uphold the reputation of the organization for delivering safe and reliable products to customers.