LQATS Corrective and Preventive Actions CAPA Architecture
The LQATS CAPA architecture identifies, investigates, resolves, and prevents issues that affect product quality or performance within a company. CAPA Architecture forms part of a broader quality management system (QMS) and systematically addresses problems, implements corrective actions to resolve them, and takes preventive actions to avoid their recurrence.
Here’s a breakdown of the CAPA architecture:
1. Data Collection & Problem Identification
- Input Data: The CAPA process starts by collecting data from various sources, including customer complaints, internal audits, employee feedback, product inspections, and system monitoring.
- Problem Recognition: Any non-conformance or deviation triggers an investigation, which may relate to product defects, process inefficiencies, or other failures.
- Initial Review: A review determines whether the issue requires corrective or preventive actions.
2. Root Cause Analysis
- Investigation: Once an issue is identified, a thorough investigation uncovers its root cause.
- Data Analysis Tools: Statistical tools and data analysis software help identify patterns or trends in the data.
3. Corrective Actions
- Action Plan Development: After identifying the root cause, the team develops a corrective action plan to address the immediate issue and eliminate its cause.
- Implementation: The team implements the corrective action to fix the issue in the system, process, or product.
- Verification: After implementation, the team verifies that the corrective action has resolved the problem and prevented its recurrence.
4. Preventive Actions
- Prevention Strategy: Preventive actions identify potential future issues and address them before they occur. This involves spotting trends or weaknesses and taking proactive measures.
- Implementation of Preventive Actions: Like corrective actions, preventive actions are implemented to reduce the risk of recurrence.
- Evaluation of Effectiveness: The preventive actions are evaluated to ensure they effectively reduce potential risks.
5. Documentation & Reporting
- CAPA Records: The system documents all CAPA activities, including investigations, corrective actions, preventive actions, and their outcomes in LQATS. This documentation is crucial for audits, reviews, and regulatory compliance.
- Tracking: LQATS tracks progress on CAPA activities, logging each action taken.
- Metrics & KPIs: Performance metrics and KPIs measure the success of the CAPA process and drive continuous improvement.
6. Review & Feedback
- Management Review: Senior management regularly reviews the CAPA process and its outcomes. They assess the effectiveness of implemented actions, identify trends in non-conformances, and evaluate overall process performance.
- Feedback Loops: The system feeds information from the review process back into the system for continuous improvement. Lessons learned refine procedures and mitigate future risks.
- Continuous Improvement: LQATS CAPA Architecture supports a continuous improvement culture, helping organizations enhance their quality management processes.
7. Software & Automation in CAPA
- LQATS CAPA Management Systems: Companies use LQATS to automate and streamline the process. LQATS provides:
- Workflow automation to trigger actions.
- Collaboration platforms for team coordination.
- Real-time tracking of ongoing tasks and issue resolution.
- Reporting and analytics tools for management insights.
- Integration with other QMS software to enhance overall quality and compliance management.
8. Regulatory Compliance
- Compliance with Standards: The CAPA process must comply with various regulatory standards. The system ensures that all actions and processes meet legal and industry-specific requirements.
Benefits of a Well-Implemented CAPA Architecture
- Improved Product Quality: By addressing root causes and preventing recurrence, the system improves product and service quality.
- Enhanced Customer Satisfaction: Effective CAPA processes resolve customer complaints and quality issues, increasing satisfaction and loyalty.
- Regulatory Compliance: The system helps maintain compliance with quality and safety standards set by regulatory agencies.
- Operational Efficiency: Streamlining issue resolution and prevention improves resource allocation and reduces disruptions.
- Risk Reduction: By proactively addressing root causes, the system minimizes the risk of future failures.
In conclusion, the LQATS CAPA architecture integrates processes to identify and resolve non-conformances, ensure continuous improvement, and maintain high-quality standards across an organization.
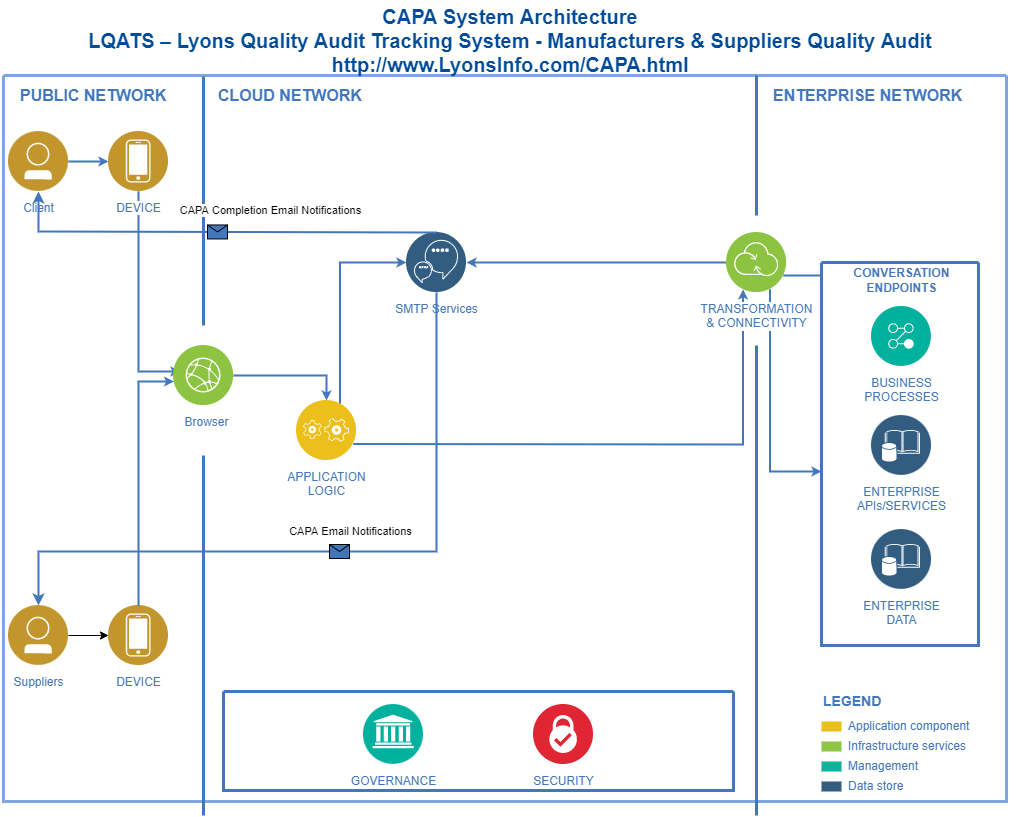
What Is CAPA?:
CAPA stands for Corrective Action and Preventive Action.
It is a systematic approach used to identify, investigate, and address issues or non-conformances in the procurement process.
CAPA plays a crucial role in maintaining quality standards within an organization’s supply chain.
Purpose of Supplier CAPA:
When a company uses products or services provided by suppliers, an effective supplier CAPA mechanism is essential.
Supplier CAPA helps investigate and correct any quality issues related to those suppliers.
It ensures that corrective and preventive actions are taken to prevent recurrence of problems.
Benefits of Automating Supplier CAPA Processes:
Automated Routing and Approval:
Software specifically designed for managing supplier CAPAs automates the routing, delivery, escalation, and approval of CAPAs and related documents.
Central Repository:
A web-based repository stores all documents related to supplier corrective actions.
This simplifies search and retrieval during audits or inspections.
Integration with Quality System:
A robust CAPA system integrates CAPA processes with the rest of the quality system.
For example, resolving a CAPA can trigger updates to standard operating procedures (SOPs) and initiate personnel retraining.
Tracking and Bottleneck Identification:
CAPA software tracks routing information and data entered into electronic CAPA forms.
This helps identify bottlenecks and understand the sequence of events during processing.
Collaboration Across Departments:
Implementing CAPA in procurement requires collaboration between different departments involved in sourcing goods or services.
Thorough investigation across the entire supply chain prevents future occurrences.
Remember, an effective supplier CAPA system ensures quality, addresses issues promptly, and contributes to continuous improvement.